CNC Aluminum Machining
Our complete CNC aluminum service will accompany your aluminum machining project from the prototype construction to the end aluminum parts manufacturing.
Professional Aluminum Machining Team
Can be manufactured around the clock, 7 days a week.
As lightweight metals are widely used, aluminum machining parts are becoming a choice of many industries. With all of our machining experience, CNC aluminum has been CncChinese’s expertise for many years.
We focus on the manufacturing of non-standard precision aluminum parts with complex structures and are committed to delivering high accuracy and consistent components to our clients. We continue to invest in new CNC machine equipment and skilled employees to ensure that our team maintains a strong competitive advantage. We have also been improving the aluminum machining process to improve efficiency and quality, and continue to meet customer production needs.
Machined Aluminum Prototypes
Before the mass manufacturing of aluminum parts, aluminum CNC prototyping is an effective way to handle complex design verification and pre-production testing. It allows you to find and solve problems faster and move towards production.
We perform an efficient, accurate, and cost-effective process in-house to provide superior product results for your aluminum prototype machining. Our engineering team will review each project, analyze your design and meet any special needs such as a combination of welding, EDM, or wire EDM processes. This in-depth validation ensures you receive the most effective machining processes for your budget, time, and materials.




Manufacturing Of Custom Aluminum Parts
If you need assistance on your custom aluminum machining projects, we will be one of the most capable and affordable production sources with our technology, experience, and skills. Our strict implementation of ISO9001 quality system standards, and the combination of efficient production processes and flexible custom engineering enable us to deliver complex projects in short turnaround times and provide excellent product quality.
We also provide typical surface treatment operations for custom aluminum parts, such as sandblasting, shot blasting, polishing, electrophoresis, chromating, powder blasting, painting, etc.
Benefits Of Using Aluminum In Machining Operations
- Benefits Of Using Aluminum In Machining Operations
- Both Strong and Lightweight
- Excellent Machinability
- Excellent Corrosion Resistance
- Greater Electrical Conductivity
- Resistant to Low Temperatures
- Surface Finishing and Anodization Potential
- Lower Production Costs
- Recyclability
5-axis CNC Milling Aluminum
CncChinese offers advanced 5-axis CNC milling aluminum, which significantly increases the range of possibilities for machining various types of aluminum parts. No matter how many parts your assembly is composed of, we can handle all kinds of aluminum milling projects that require high precision and complex shape machined parts, and provide extremely tight tolerances and excellent surface finish to meet your most difficult manufacturing challenges.
Advantages of 5-axis Milling Aluminum
The machine is on 5 sides of a part with one single setup. Saves set up time, increasing machining productivity.
Higher accuracy and outstanding surface finish, improving overall part quality.
Workpieces are not moved through several workstations, reduces error and fixturing costs, less time hand benching in a CNC router.
Milling and drilling with compound angles. Improved tool life and cycle time as a result of tilting the tool/table to maintain optimum cutting position and constant chip load.
Shorter and more rigid tools may be used. Higher spindle speeds and feed rates may be achieved on the CNC router while reducing the load on the cutting tool.


5 Steps To Improve Dimensional Stability In CNC Aluminum
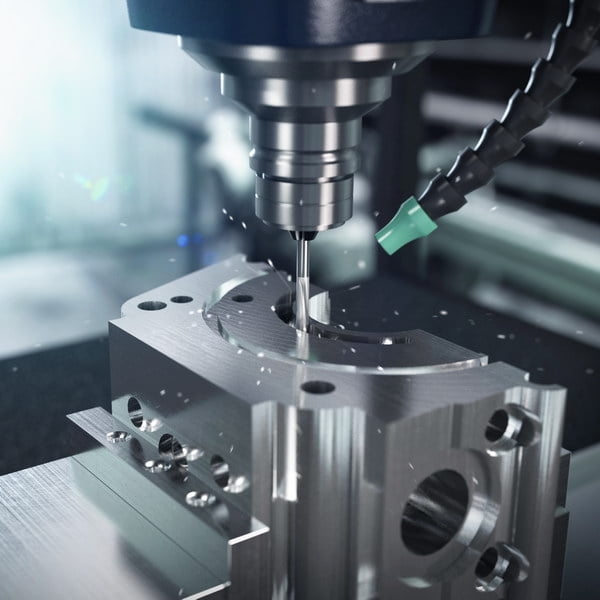
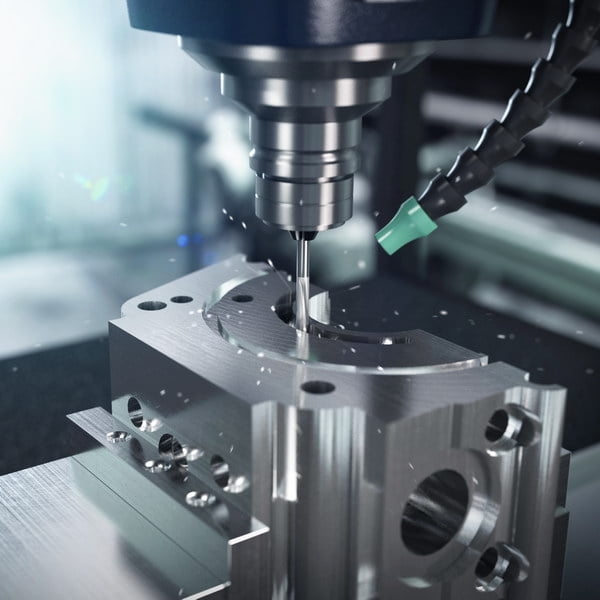
Eliminate the internal stress of the material
The common way to eliminate internal stress is to use natural or artificial aging and vibration treatment. Secondly, Cutting the excess parts in advance and continuing to process after 1-2 hours of natural aging can also eliminate the deformation caused by internal stress.
Improve the clamping method of the workpiece
For the CNC mill processing of thin-walled aluminum parts with poor rigidity, the following clamping methods can be used to improve the machining accuracy: Use suction cups to distribute clamping force evenly along with the thin plate; Fill the inside of the workpiece with a medium to improve rigidity.
Improve the cutting ability of the tool
The material and geometric parameters of the tool have an important influence on the cutting force and cutting heat. The correct selection of the tool is essential to improve dimensional stability.
Choose a reasonable machining process
Choose a reasonable machining process
The CNC high-speed machining process is generally: rough machining – semi-finish machining – clear corner machining – finishing. For parts with high precision requirements, it is necessary to increase the number of semi-finishing machining and retain a uniform machining allowance.
Use appropriate methods of operation
Choose the right feed speed, spindle speed, and cutting depth; Symmetrical machining for the front and back of the workpiece; Multi-layer machining for all cavities of the workpiece; Use drilling and then milling when machining parts with a cavity.


Challenges Faced When Starting Your CNC Aluminum Project
Aluminum CNC Machining Services Offered, Contact Now!
- Aluminum alloy type that meets the function of the product;
- The rigidity of the machine can carry enough cutting loads;
- The right range of cutting parameters for a given tool in a given material;
- Solve the problem of clearing chips and cooling;
- Use special fixtures to achieve high-precision and consistent machining.
Integrated Machining Process Of Aluminum Parts


Generally, aluminum CNC machining is not a standalone production process. When short-run production needs reach hundreds or more, you need a complete solution to achieve a more efficient, accurate and cost-effective process.
When manufacturing aluminum parts, we review each project based on the complexity and manufacturability of the part, evaluate the production cost, and create a process route that meets your design and specifications.
We have combined 3-axis, 4-axis and 5-axis CNC milling, CNC turning and other manufacturing processes to expand the manufacturing capabilities of the aluminum alloy prototypes, accommodate any challenge with ease, and save time and cost. These optimized process combinations include traditional process technologies such as EDM, Wire EDM, Die Casting, Investment Casting, Aluminum Extrusion, and Forging.
Aluminum Material Grades We Work With
Aluminum alloys have a wide range of properties, such as flexibility, weldability, high strength to weight ratio, corrosion resistance, lightweight, electrical conductivity, and excellent anodizing surface finishing. Due to its low cost and formability, aluminum is widely used in industrial areas. The type of aluminum grade you ultimately choose depends on the intended use of your aluminum parts in the manufacturing project.


Aluminum 6061
The most versatile of the heat-treatable aluminum alloys, while keeping most of the good qualities of aluminum. This grade has a great range of mechanical properties and corrosion resistance. It can be fabricated by most of the commonly used techniques and it has good workability in the annealed condition.
Aluminum 6082
Aluminum 6082 is a medium strength alloy with excellent corrosion resistance. It has the highest strength of the 6000 series alloys. 6082 is known as a structural alloy. In plate form, 6082 is the alloy most commonly used for machining. As a relatively new aluminum alloy, the high strength of aluminum 6082, such as high tensile strength, has allowed it to replace aluminum 6061 in many applications.
Aluminum 6063
Commonly known as an architectural alloy. It has reasonably high mechanical properties, excellent finishing characteristics and a high degree of resistance to corrosion. Most often found in various interior and exterior architectural applications and trim. Aluminum 6063 is used for aluminum extrusion applications.
Aluminum 7075
Aluminum 7075 is one of the highest strength aluminum alloys available. It has an excellent strength-to-weight ratio, and it is ideally used for highly stressed parts. 7075 aluminum is a typical material used in the aviation industry with complex structure and high precision.
Aluminum 2024
Aluminum 2024 is used in applications requiring high strength to weight ratio, as well as good fatigue resistance. It is not weldable and has average machinability. 2024 has poor corrosion resistance, not quite suitable for anodization.
Aluminum 5052
This is the highest strength alloy of the more non-heat-treatable grades. Its fatigue strength is higher than most other aluminum grades. It has good resistance to the marine atmosphere and saltwater corrosion and excellent workability.






We will Continue to Forge Ahead in CNC Aluminum Machining
Whether you require machined aluminum prototypes or custom aluminum parts for your automotive, aerospace applications or medical device component, we can easily help you. With our expertise in CNC aluminum machining and the ability to integrate external combined processes, we can ensure the best performance for your machining aluminum projects.